Discover the Advantages of Choosing the Best Press Brake for Your Manufacturing Needs
In the fast-paced world of manufacturing, choosing the right equipment is crucial for ensuring efficiency and precision. One essential machine in this industry is the press brake, which plays a vital role in bending and shaping metal parts with accuracy. According to a recent report by Markets and Markets, the global press brake market is projected to reach $3.5 billion by 2026, growing at a CAGR of 3.8% from 2021 to 2026. This surge underscores the importance of selecting the best press brake to meet specific manufacturing needs, as it directly impacts productivity and quality. By investing in advanced press brake technology, manufacturers can not only improve their operational capabilities but also adapt to changing market demands and enhance their competitive edge. Understanding the advantages offered by various press brake models can thus be a game-changer for any manufacturing business striving for excellence.
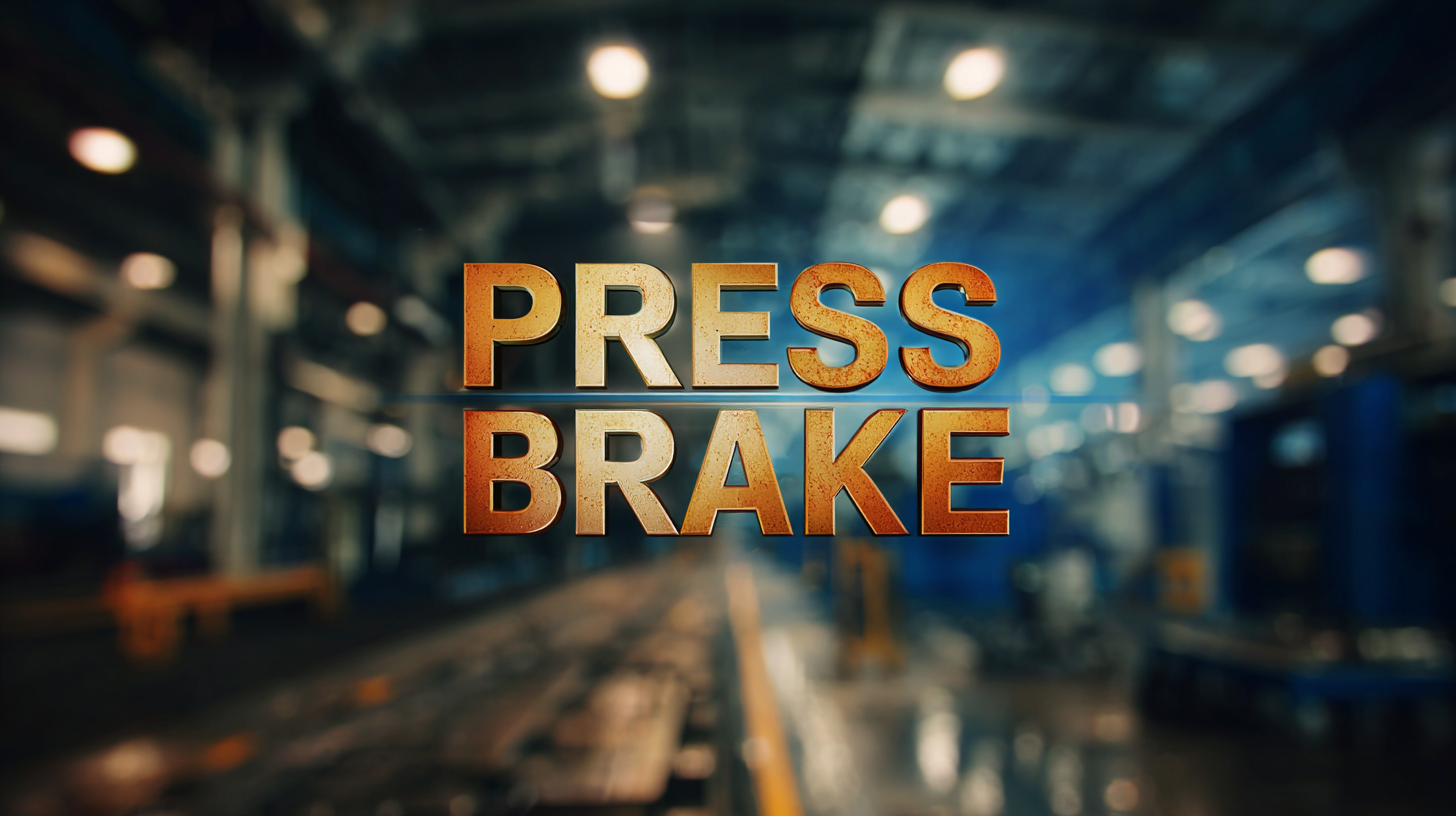
Understanding Press Brakes: Key Technical Specifications to Consider
When selecting the best press brake for your manufacturing needs, understanding key technical specifications is essential. Press brakes are versatile machines that require careful consideration of throat depth, bending capacity, and tooling options. According to a recent industry report by Technavio, the global press brake market is expected to grow by 4.5% annually, indicating rising demand for high-quality machines tailored to specific applications. Choosing a press brake with the right tonnage for your projects can maximize efficiency and minimize operational costs.
Tips for selecting a press brake include analyzing required bending lengths and materials. It's crucial to assess whether a conventional or hydraulic press brake suits your production line. Hydraulic systems offer superior precision and adaptability, which are vital when dealing with various materials such as aluminum, steel, and plastics. Moreover, considering automation features, such as CNC controls, can significantly enhance productivity. A McKinsey survey highlighted that manufacturers incorporating advanced automation saw a 20% increase in throughput and a 30% reduction in downtime.
Furthermore, pay attention to the machine's overall build quality and safety features. Invest in models with robust guarding systems and ergonomic designs to protect operators. In compliance with OSHA standards, regular training on safety procedures can help maintain a secure working environment while optimizing equipment performance.
The Importance of Precision: Tolerances and Their Impact on Production Quality
When it comes to manufacturing processes, precision is not just a luxury; it is a necessity. The tolerances set during production directly affect the quality and durability of the final product. Using a high-quality press brake allows manufacturers to achieve tighter tolerances, which, in turn, reduces the likelihood of defects and rework. This level of precision ensures that parts fit together seamlessly, enhancing overall product performance and reliability.
Moreover, the impact of tolerances extends beyond individual components. In industries where safety is paramount, such as aerospace and automotive sectors, even the slightest deviation can compromise integrity. Investing in the best press brake technology means equipping your facility with machinery that can maintain consistent tolerances, thereby adhering to stringent industry standards. As manufacturing systems strive for excellence, the importance of precision and the right equipment becomes glaringly evident. By selecting a press brake that meets your specific production needs and tolerances, you lay the groundwork for improved quality and sustained competitiveness in the market.
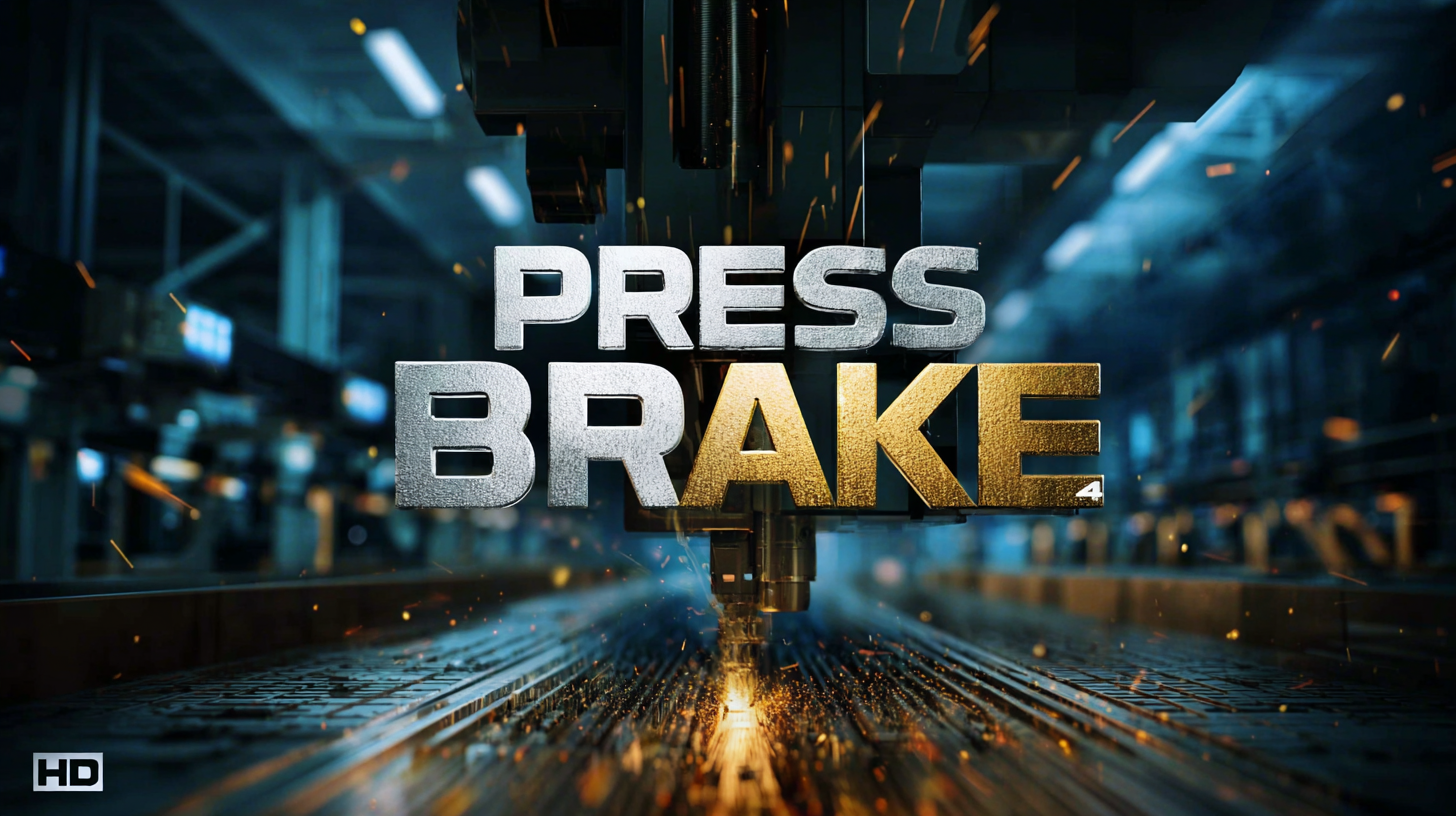
Evaluating Power Requirements: Hydraulic vs. Mechanical Press Brakes
When evaluating the power requirements of press brakes, manufacturers often face a critical choice between hydraulic and mechanical options. According to a report by Smithers Pira, hydraulic press brakes dominate the market, accounting for over 60% of global press brake installations. Their ability to exert consistent force and handle thicker materials makes them an attractive choice for heavy-duty applications. Hydraulic systems provide higher tonnage capabilities, ensuring precision and accuracy in bending operations, particularly in high-stress environments.
On the other hand, mechanical press brakes offer a more efficient operation for lighter materials. The same report indicates that mechanical models have become increasingly popular among manufacturers looking to reduce energy costs, as they typically consume less power compared to their hydraulic counterparts. They also allow for faster cycle times, which can significantly enhance productivity on the shop floor.
**Tip:** When choosing between hydraulic and mechanical press brakes, consider not only your current manufacturing needs, but also potential future requirements. **Tip:** Always assess the total cost of ownership, including energy consumption and maintenance, to ensure you select a press brake that aligns with your operational goals.
Discover the Advantages of Choosing the Best Press Brake for Your Manufacturing Needs - Evaluating Power Requirements: Hydraulic vs. Mechanical Press Brakes
Feature | Hydraulic Press Brake | Mechanical Press Brake |
---|---|---|
Power Source | Hydraulic fluid power | Mechanical linkage |
Force Control | Variable force control | Constant force throughout stroke |
Speed | Slower overall speed | Faster operation |
Maintenance | Requires regular fluid checks | Generally lower maintenance |
Cost | Higher initial investment | Lower initial investment |
Precision | High precision, especially for thick materials | Good precision, best for thinner materials |
Advanced Features: CNC Technology and Automation in Modern Press Brakes
The modern manufacturing landscape is rapidly evolving, and one of the key components driving this change is the implementation of advanced features like CNC technology and automation in press brakes. These innovations not only enhance precision but also significantly increase productivity. By integrating Computer Numerical Control (CNC) technology, manufacturers can achieve higher accuracy in bending operations, ensuring that parts are produced consistently and to required specifications. Automation further streamlines the production process, reducing the need for manual intervention and allowing for quicker turnaround times on projects.
When selecting the best press brake for your manufacturing needs, consider investing in models with advanced CNC features. Look for options that offer programmable bending sequences, which can save time and reduce the potential for errors during operations. Additionally, check if the machine supports automated setup processes, as this feature can greatly enhance efficiency, especially in high-volume production settings.
Tip: It's essential to evaluate the versatility of the press brake you choose. A machine capable of handling various materials and thicknesses will provide better adaptability for future projects. Moreover, consider attending demonstrations or requesting trials to observe how automation and CNC technology can optimize your specific workflow.
Advantages of Advanced Features in Modern Press Brakes
Cost-Benefit Analysis: Investing in Quality Press Brakes for Long-Term Savings
When it comes to manufacturing, the choice of equipment significantly impacts both productivity and cost-efficiency. A cost-benefit analysis reveals that investing in top-tier press brakes can lead to substantial long-term savings. According to a recent report by the Fabricators & Manufacturers Association (FMA), high-quality press brakes can increase operational efficiency by up to 30%, reducing the time and labor costs associated with manufacturing processes. This efficiency translates into a lower cost per unit, allowing manufacturers to maintain competitive pricing without sacrificing quality.
Tip: Prioritize features such as precision control and adaptability when selecting a press brake. These qualities not only ensure better accuracy in forming but also reduce material waste, which can lead to further cost reductions over time.
Moreover, the initial investment in a premium press brake pays off through durability and fewer maintenance requirements. According to a study published by the Association of Equipment Manufacturers (AEM), companies that opted for quality machines saved, on average, 15% on long-term maintenance costs compared to those who chose budget alternatives.
Tip: Consider the total cost of ownership (TCO) rather than just the purchase price. Assessments should include energy efficiency, maintenance expenses, and expected lifespan to determine the most economically viable option for your manufacturing needs.
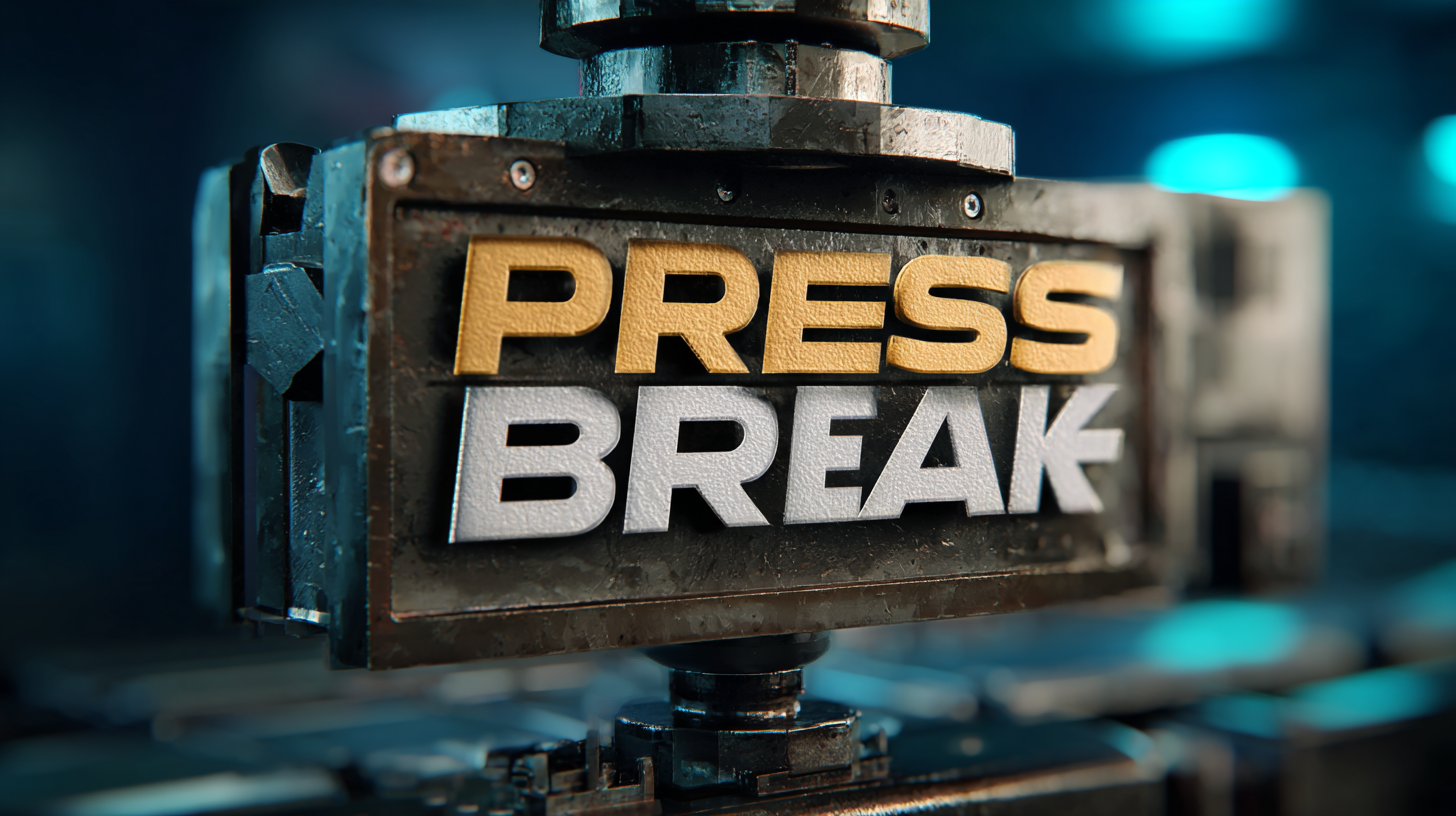